روزنامه بین المللی در مورد پژوهش وتوسعه حداقل رساندن نقص های لوله های پلاستیکی ام- ناراسیم ها دانشکده مهندسی دانشگاه مهندسی صنعتی باهایردر آر- رجی کومار دانشکده مهندسی و دانشگاه مهندسی صنعتی باهایردر ایپژوهش جهت کشف عوامل ریشه ای وقوع نقص ها و ضایعات در فرآیند اکستروژن (روزن رانی) نرم یک روش سیستماتیک ارائه میدهد. در این خصوص مسائلی مانند زبری و خراش سطح، برآمدگی، علائم نشست، ضخامت ناهموار دیواره لوله، اختلاف ابعاد، مسئله کانونی به عنوان نقص مشخص شده است. جهت مشخص کردن علل ریشه ای این قبیل نقصها (نقصهای مذکور) از دیاگرام یا الگوی علت و معلولی استفاده میشود. با استفاده از این دیاگرام درمییابیم که علل ریشه ای و اصلی هر نقص پارامترهای فرآیند اکستروژن (روزن رانی) میباشند. مانند فشار خلاء، دما، سرعت خیز، سرعت پیچ در فرآیند اکستروژن (روزنرانی) و خواص مواد خام. براساس اطلاعاتی که شرکتها در اختیار قرار میدهند حدود 758/76 درصد عللهای ریشه ای فوق الذکر ناشی از عملکرد اپراتورهای آن میباشند. که از قرار گرفتن نامناسب پارامترهای فعال ناشی میشود. بیشترین دفعات وقوع این نقصها را میتوان با استفاده از جدول پارتو (Pareto) مشخص نمود. پس از شناسایی این گروه از نقصها که به دفعات بیشتری رخ میدهند و با استفاده از روش تاکوچی (Taguchi) یا مهندسی کیفیت که در بهینه ساختن موقعییت پارامترهای پردازش در تولید پلاستیک استفاده میشوند. موفق شدند تا با کاهش نوسانات تولید (کیفیت) با توجه به ارزش هدف وقوع این نقص ها را به حداقل خود برساند. شرکت آبیاری Berhu Tesfa و شرکت تکنولوژی آب PLC (BTFWTPLC) را به عنوان نمونه انتخاب کردند تا تابع ضرر کیفیت به انضمام روش تاکوچی (طرح آزمایشی) را در خصوص برخی از محصولات گزینه شده این شرکتها بکار بگیرند. خصوصاً با استفاده اصل تابع ضرر تاگوچی، ضرر کیفیت ناشی از تغییر عملکرد فعلی مورد محاسبه و الزام آن در جهت توسعه مورد تأیید قرار گرفته است. در این رابطه از طراحی آزمایشی به منظور بهینه سازی پارامترهای پردازش چهار محصول برگزیده استفاده شده است، که این چهار محصول از میان لوله های 50 mm HDPE1Ø و لوله ساده ی 25mm Ø انتخاب شده اند. چهار پارامتر مستقل پردازش مورد بررسی قرار گرفت که با ذکر نام عبارتند از : فشار خلاء-سرعت خیز-سرعت پیچ- حرارت که برای DOE در نظر گرفته شده اند. ازنرم افزار تجاری مینی تب (minitab15) برای تجزیه و تحلیل این آزمایش استفاده شده است که خود مبتنی بر نتیجه ی ناشی از تحلیل بهینه سازی پارامترهای پردازش انتخاب شده میباشد. در اینجا قبل از استفاده از طراحی آزمایشی به محاسبه و مقایسه تابع زیان ومیزان ضرر کیفیت با یکدیگر پرداخته و از این طریق متوجه شدند که استفاده از روش تاگوچی یا به عبارتی طراحی آزمایشی میزان ضرر و زیان کیفیت ناشی از انحراف عملکرد راتا`201/85 درصد برای محصولات برگزیده بهبود بخشیده .هم چنین در اینجا آزمون ساختاری خواص مکانیکی لوله ی اصلی با استفاده از دستگاه جامع آزمایش مورد بررسی قرار گرفت (خواص کششی و فشار هیدرواستاتیکی) و از آن دریافتند که خواص و ویژگی های محصول پلاستیک (نرم) با توجه به کاربرد هدف که برای آن در نظر گرفته شده بدون آن که شکست بخورد حفظ می شود . علاوه بر این به منظور حداقل رساندن نقص های ناشی از خواص غیر خطی (مانند پوسته پوسته شدن، شکست ذوب و تورم اکسترود) مدل سازی ریاضی و محاسبه ی تحلیلی را ساخته و ارائه گردید. از این رو بهترین پارامترهای عملیاتی را تعیین کردند که شامل حداکثر فشار، زمان اقامت، گشتاور عملیاتی موردنیاز و سرعت پیچ شدن اکسترودر میباشند. مقدمه پلیمرها از مزایای متعددی برخوردار هستند که از میان آنها میتوان به وزن سبک، طراحی قابل ارتجاع و ایزولاسیون الکتریکی آنها اشاره کرد ضمن اینکه از هزینه ساخت نسبتاً کمی برخوردار می باشند. از مزایای پلیمرهای حساس نسبت به سایر مواد مانند فلزات این است که ازقابلیت بالاتری برخوردار است. بنابراین غیر منطقی نیست اگر پیش بینی کنیم که پلیمرها در آینده بخش وسیعتری از کل بازار مواد را به خود اختصاص خواهند داد شکل (1). pic 1 صنایع در تولید مواد پلاستیکی، میزان قابل توجهی از ضایعات را تولید میکنند. پلاستیکهای اسقاطی حاصل ساخت و بسته بندی محصولات پلاستیکی و همچنین مواد ساخته شده میباشند. تولیدکنندگان پلاستیک در خصوص تولید این قبیل ضایعات و وقوع برخی از مشکلات اجرایی پاسخگو می باشند. بنابراین برای تولید کنندگان میزان ضایعات تولید شده توسط طراح های صنعتی پلاستیک به شدت هزینه ساز بوده که می تواند به سلب اعتماد مشتریان نسبت به محصولاتشان میشود. اولین و تنها راه حل این مشکلات تحلیل و کاهش میزان ضایعات در منبع ایجاد آن و بهبود عملکرد محصولات می باشد. بعنوان نتیجه اثر این تز به شدت روی کاهش تولید ضایعات و بهبود کارآیی عملکرد متمرکز می شود. که آن را خصوصاً با تمرکز روی کارخانه ی پلاستیک Berhu Tesfa می توان مشاهده کرد. زیرا وقتی شما کارخانه ی را در حال تولید بازدید می کنید و محصولاتی را می بینید که روی زمین قرار گرفتند که دارای ضایعات زیادی در سطح داخلی و بیرونی محصول میباشند و ماشینی را مشاهده میکنید که روزانه بدون وقفه مشغول خرد کردن ضایعات میباشد حاکی از این است که میزان ضایعات بیش از حد انتظار بوده و باعث بالا رفتن هزینه بازسازی کارخانه میگردد. این مسئله باعث میگردد که تولیدکنندگان سهم خود را از بازار و مشتریانشان از دست داده و با رقبای خویش جایگزین گردند. اینطور برآورد شده است که هزینه مواد قابل استفاده در تولید اکستروژن 50 تا 70 درصد هزینه کل را شامل میشود . که این رقم با در نظر گرفتن هزینه های کارگران میتواند به رقمی بین 60 تا 80 درصد متغیر باشد. هر تکنیکی که بتواند هزینه های کارگری را کاهش، میزان ضایعات مواد را حداقل و دستیابی به کیفیت موردنیاز را میسر کند بدون تردید یک عامل مهم و قابل توجه میباشد (2). تحقیقات در این مورد با شناسایی و تحلیل ضایعات (مسائل کمی) و همچنین مشاهده ی عملکرد محصولات از کارخانه تا محوطه کار شروع میگردد. و این مشکلات کیفی را با استفاده از ابزارهای فنی معروف کیفی ساز بهینه کرد که به آن روشهای تاگوچی یعنی طراحی آزمایشی گفته میشود. برای کالاهای برگزیده, تابع ضرر تاگوچی را قبل و بعداز کاربرد ابزار موردنظر در کنار استفاده ی تنگاتنگ نرم افزار مینی تاب (Mini Tab)5 برای تحلیل برآورد میشود. این فرآیند شامل ترتیب ذیل میباشد. گرمایش و ذوب پلیمر، مکش پلیمر به واحد، شکل دادن مواد مذاب در شکلهای و ابعاد موردنیاز، خنک کنندگی و جامد ساختن آنها، کیفیت خوب و اکتسروژن (روزنرانی) زمانی به طور مطلوب صورت میگیرد که شرایط طراحی از سرعت و دمای چرخشی ثابت پیچ و ترکیب یکنواخت برخوردار باشد. برای یک اکسترودر طراحی شده و ارائه شده، کیفیت بد اکتسرودر را میتوان به قرار گرفتن نامناسب شرایط پردازشی مرتبط ساخت. مرور مد داک (Mad doc) در نوشته های خود به منظور نشان دادن اینکه چگونه موقعیت نامناسب شرایط پردازشی بر کیفیت تولید اثر میگذارد، به مسئله ضرورت وجود کیفیت برای اکستروژنی با داشتن پوسته ای به ضخامت 10 mm اشاره میکند. گرانروی (Viscosity) به واسطه ی وجود اختلاف دما تحت تأثیر قرار میگیرد و اختلافات گرانروی (Viscosity) در جهت تولید تغییرات فشار عمل کرده و نهایتاً سبب ایجاد تفاوت های ضخامتی میشود. سطح بالای اکستروژن و کیفیت خوب آن غالباً در نهایت مطلوب میباشند که آنها را از هم غیرقابل مقایسه میکند. تادمور (Tadmor) و کلین (Klein) (5) ترکیب نادرست عناصر تشکیل دهنده ی یک محصول را که میتوان به شکل نادرست و محصول غیر یکنواخت منجر شود، طبقه بندی میکنند. کیفیت ضعیف اکستروژن (گرانروی) یک اکسترودر مشخص خیلی اوقات به وجود اختلافات تصادفی در دما – فشار و سرعت عملیات مربوط میشود. براساس گزارش داد (Dawd 6) و یانگ (Young 7) خواص تولید به دمای اکسترودیت (روزنرانی) بستگی دارد. فنر (Fenner) و همکاران نیز یبان کردند از آنجایی که خنک سازی پیچ موجب کاهش عملکرد میشود بنابراین حذف این نوسانات بدون استفاده از عمل خنک سازی پیچ این امکان را برای اکستروژن (روزنرانی) فراهم میکند تا به بالاترین سطح بازدهی خود برسند. و متخصصان اکستروژن (روزنرانی) بیان میکنند که 5 عامل کیفیت و عملکرد محصول را محدود میکند که عبارتند از : قدرت وسرعت پیچ دادن، دما، خوراک فشارخلاء و فرآیند زیرآب. برنامه ریزی پژوهش در این مورد، طرح آزمایشی به منظور مطالعه ی تأثیر عوامل (پارامترهای پردازش) در فرآیند اکستروژن (روزنرانی) پلاستیک مورد استفاده قرار گرفته از آن جهت که علل اصلی ایجاد نقص در تولیدات محسوب میشوند از این رو محصولاتی مانند لوله ی پلی اتیلن HDPE به ضخامت 50 mm و لوله ی ساده به ضخامت 25 mm همانطور که در شکل 2 آمده انتخاب شده اند. pic 2 شکل 2: محصولات نمونه 2.1 نقص در فرآیند اکستروژن (روزنرانی) به هر نوع خطاء در ویژگی های تولید اطلاق میگردد که نسبت به معیار تنظیم شده توسط فرآیند ساخت به وجود بیاید. این نقص میتواند یا از یک منشاء جداگانه به وجود آید یا اینکه در هر مرحله ای از فرآیند تولید متأثر از تأثیر چند عامل ایجاد شود. نقصها و شکست های معمولی که غالباً در فرآیند اکسترژن پلاستیک (روزنرانی) رخ میدهد به سه عامل اصلی بستگی دارد که عبارتند از: طراحی قطعه و قالب، انتخاب مواد و پردازش. در بسیاری از موارد این قبیل شکست ها و یا عدم موفقیت ها در طول فرآیند پردازش رخ میدهد که خود آن باعث ایجاد نقصهای دیگری میشود که در قطعات اکسترود میتوان یافت مانند Warpage، علامت نشست تنش پسماند، دریچه یا گیر هوا، خط جوش، صافی کم، جلای متغیر سطح، سطح خالدار، نوسان ولتاژ اکسترودر، تغییر ضخامت و ضخامت ناهموار دیواره، تغییر نوسان ابعاد، مشکل کانونی که همانطور که در تصویر شماره 2 نشان داده شده در تولید اکستروژن (روزنرانی) نقصهای معلول تولید شامل عوامل زیر میشود: درک نادرست از روش پردازش، استفاده نادرست از ماشین آلات قدیمی، فقدان کارکنان آموزش دیده، شکستگی ماشین آلات و فضا نامناسب کاری. pic 3 تصویر 3: نقصهای مشاهده شده • زبری سطح • علائم • برآمدگی • نوسانات ابعادی • خارج از نوبت • علائم نشست در اینجا اطلاعات گردآوری شده که حاصل گزارشات و مشاهدات عینی کارکنان کارخانه در این بخش خاص میباشد ارائه و مورد تجزیه و تحلیل قرار میگیرد تا متعاقب آن عملکرد صحیح اتخاذ، پیشنهاد و در نهایت توسعه یابد. 2.2 شناسایی نقص اصلی تولیدات تمام نقصهایی که در عرض 6 ماه در گروه خاصی از تولید رخ میدهد، گزارش میشود و با استفاده از جدول پارتو (Pareto) مورد تجزیه و تحلیل قرار میگیرد تا به کمک آن بیشترین دفعات وقوع را شناسایی کنیم. در مورد این نقص اصلی اکستروژن که در یک تولید خاص به وجود میآید، یک تحلیل کامل با شرح جزئیات ارائه شده است. pic4 تصویر 4: جدول پارتو (Pareto) برای نقصهایی که به دفعات در تولیدات لوله رخ میدهد. • نمونه ای از نقصه ای کیفی • (A) ضخامت ناهموار دیواره • (B) (خارج از مرکز) مشکل کانونی • (C) نوسان ابعادی • (D) علائم نشست • (E) خراش • (F) عدم پیوستگی • (G) خمیدگی • (H) پرداخت ضعیف سطح 63/3 %بالاترین درصد وقوع نقص به شمار میآید و بیانگرآن است که نقصه ایی که در تولیدات لوله رخ می دهدعبارتند از نوسان ضخامت جداره لوله، شکل کانونی (خارج از مرکز) و نوسان ابعادی . در این مورد برای به حداقل رساندن این نقصها بیشترین توجه به آنها جلب شده است. در تولیدات لوله نقص هایی ذیل نقص هایی هستند که به دفعات بیشتری اتفاق میافتند و آنها عبارتند از ضخامت غیر یکسان دیواره، مشکل کانونی و نوسان ابعادی از میان این نقصها، وقتی ما به بررسی سطح تأثیر آنها روی میزان رضایتمندی مشتریان و افزایش هزینه تولید میپردازیم، متوجه میشویم که دو عامل نوسان ابعادی و نوسان ضخامت دیواره از سوی شرکتها به عنوان اصلی ترین نگرانی در نظر گرفته شده است. در نتیجه بیشترین توجه به این گروه تولیدی معطوف گردیده تا بدین وسیله نوسانات ابعادی لوله های HDPE به ضخامت دیواره 50 میلیمتر و لوله ها ساده ی با ضخامت 25 میلیمتر را کاهش دهند. این محصولات از آن جهت که بیشترین تولید را به خود اختصاص میدهد به عنوان نمونه انتخاب شدند. 2.3.X جدول تحلیل محصولات برگزیده از میان اطلاعات گردآوری شده در مورد هر محصولی که مورد مطالعهی ما قرار گرفته است جدول تحلیل – X در مورد چند نمونه توسعه یافته است تا به طور دقیق نشان دهد که آیا فرآیند تولید خارج از حد یا خارج از کنترل بوده یا خیر. pic4 تصویر 5: نقصهای مشاهده شده و لوله ساده با ضخامت 25 میلیمتر را نشان میدهد. 3. تحلیل فقدان کیفیت جهت تعیین تأثیر پارامترهای پردازش از میان نتایج که از تحلیل داده های پارتو (Pareto) و جدول X که از بخش های مذکور بدست آمده، نوع و دفعات وقوع این اشکالات در محصولات مورد نظر تعیین گردید. تابع ضرر تاگوچی جهت محاسبه میزان ضرر کیفی تولیدات منتخب به مرحله ی عمل رسید. 3.1 انتخاب پارامترهای پردازش برای محصولات (تولیدات) برای دستیابی به تولید با کیفیت، شرایط بهینه سازی تولید برای اکسترودهای مختلف با یکدیگر متفاوت می باشد . بنابر آنچه که در بالا به آن اشاره شد برای کاهش نقص های موردنظر، پارامترهای اصلی پردازش را باید انتخاب کرد که عبارتند از: زمان اقامت، منطقه بندی دما، سرعت پیچ کردن، فشار خلاء و زمان خنکسازی. در این مورد، این پژوهش تأکید خود را روی فشار خلاء، سرعت خیز، سرعت پیچ شدن و وضعیت منطقه بندی دما معطوف میسازد که با آن دستیابی به تولید با کیفیت و ایجاد وضعیت ثابت برای سایر پارامترها میسر میشود. برای لوله پلی اتیلنی چگالی بالا (HDPE Ø 50/3.0/10 bar PE-100) ابعاد داخلی و ضخامت ناهموار دیواره لوله، به عنوان ارزش هدف و ارزش پاسخگو تلقی میشود. برای لوله های ساده (IR Ø 25/1.8/16 bar PE-100) پارامترهای پردازش که در آزمایش این محصول نام برده مورد استفاده قرار میگیرد عبارتند از: -1فشار خلاء 2 -سرعت دور گرفتن 3-حرارت در حالیکه ابعاد داخلی و ضخامت دیواره معیارهای کارایی میباشند. 3.2 محاسبه اتلاف کیفیت در این مقاله برای تجزیه و تحلیل و تأیید تصمیماتی که برای بهینه سازی پارامترهای شاخص پردازش که کیفیت محصول شرکتها اثر میگذارد، از بهترین مشخصه ی سنجش عددی اتلاف کیفیت استفاده شده است. در اینجا برای اینکه بتوانیم با استفاده از تئوری تابع ضرر تاگوچی تابع ضرر را برای تعدادی از محصولات انتخاب شده برآورد کنیم از ارزش L هزینه شکست استفاده شده که از جدول زیر اقتباس شده است. pic5 جدول 1: جزئیات تولید شش ماهه این شرکت هر ماه مقادیر زیادی دچار ضرر و زیان میشود و هزینه کل باید در بازار کنونی اتیوپی ضرب گردد که به اختصار در جدو شماره 2 بیان شده است. فرمول کلی که از آن برای برآورد هزینه شکست کلیه محصولات انتخاب شده استفاده میشود عبارت است: هزینه شکست= هزینه تولید (birr/pc) – (مجموع تولید (kg/pc) * قابل بازسازی% هزینه مواد خام* (birr/kg) pic6 جدول 2: هزینه شکست تولیدات نمونه در واحد یا در وزن برای محاسبه اتلاف کیفیت باید تعدادی مفروضات را تنظیم شود که عبارتند از: • هزینه شکست = هزینه تولید-هزینه اندوخته از بازسازی ضایعات • وقوع حداکثر ضرر و زیان در دو دامنه ی متغییر . • حد تغییرات =TL / ارزش هدف=m / ارزش نمونهها=M / انحراف استاندارد = SD / هزینه شکست تولید = L 3.2.1 لوله پلی اتیلن با چگالی بالا (HDPE Ø 50/3.0/10 bar PE-100) SD= 0.25 M=44 mm TL=44±0.5 mm and L= 2.484 birr اطلاعات به دست آمده (هزینه های شکست تولیدات مورد نظر و ضایعات بازسازی شده)بدین ترتیب این ضرر برای هر محصول به شکل زیر محاسبه میگردد: L (y) = K (y-m)2= 2.484 = K (44.5 – 44)2 K= 9.936 بنابراین معدل اتلاف کیفیت برای این محصول خاص عبارت است از: L= 7199 Birr pc) 3.2.2لوله ساده با ابعاد (25/2/16 bar PE-100) SD= 0/1932, μ= 20/0893 mm / m = 21 mm, L= 1.03 birr TL= 21± 0/3 mm L (y) = K (y-m)2= 1.214 = K (143-14)2 K= 13.44 بنابراین معدل تابع ضرر کیفیت برای این محصول خاص عبارت است از L= 0/468 Birr/pc 3.3طراحی آزمایشی با استفاده از طرح ارائهای تاگوچی که طرح آزمایش توابع میباشد میتوان در یک مجموعه فشرده از آزمایشات تعدادی از پارامترهای متفاوت را که روی ویژگی های تولید اثر میگذارند آزمایش کرد. پس از اینکه پارامتری بر فرایند موثر واقع شد، می تواند به صورت مشخصی کنترل شود، سطحی که باید در آن پارامترهای متنوعی اعمال شود باید تعیین شود. پارامترهای فرآیند در نظر گرفته شده در DOE در فرایند تولید شرکت کیس، شامل فشار خلاء ، سرعت دور گرفتن، سرعت پیچ و دما است.اما اینجا بر درجه حرارت تاکید بیشتری داریم. جدول 3 جزئیات آزمایش را نشان می دهد. pic7 جدول 3: پارامترهای مورد استفاده برای انجام آزمایش ها (DOE) برای داده های به دست آمده از آزمایش برای هر محصول انتخاب شده، میانگین پاسخ و نسبت سیگنال به نویز (S/N) داده و تحلیل شدند. که معادله مشابه نسبت S/N مربوطه برای (NTB) به صورت زیر داده می شود: pic8 4. نتیجه و بحث 4.1. لوله پلی اتیلن با چگالی بالا(HDPE Dia50/3/ 10bar PE- 100) pic9 شکل 6: لوله پلی اتیلن با چگالی بالا شکل 6. پاسخ متغیر (قطر داخلی) و ابعاد نومینال شرکت ها( 44.0 mm ) را نشان می دهد. از نمودار فوق مقدار فشار خلاء 1برابر 58.5- ، سرعت دور گرفتن 2برابر 1.6، مقدار درجه حرارت 3برابر 135، درجه حرارت 4 برابر 145، درجه حرارت 5برابر 150، درجه حرارت 6برابر 165،درجه حرارت 7 برابر 160و درجه حرارت 8 برابر 165 است.این ها پارامترهای فرایند هستند که برای تولید لوله HDPE نزدیک به مقدار مورد نظر استفاده می شود. برای انتخاب بهینه پارامترهای فرایند نیاز است اثر آن روی نسبت S/N در نظر گرفته شود. پاسخ نسبت S/N باید بزرگ باشد یا به طور قابل توجهی برای هر نوع طراحی تحلیل آزمایش به حداقل نرسد. در این مورد در شکل زیر مقدار فشار خلاء 1برابر 50.5- ،سرعت دور گرفتن 2 برابر 1.8، درجه حرارت 3 برابر 125، درجه حرارت 4 برابر 145،درجه حرارت 5 برابر 150، مقدار درجه حرارت 6 برابر 155، مقدار درجه حرارت 7 برابر 160و درجه حرارت 8 برابر 165 میباشد که باعث میشود پاسخ نسبت سیگنال به نویز بیشتر از پارامترهای دیگر شود. بنابراین،بهتر است پارامتر بهینه عملیاتی پردازش و مقدار میانگین پاسخی که به مقدار مورد نظر نزدیکتر است ، بزرگ است و یا نسبت سیگنال به سهمیه در آن کمتر است، انتخاب شود. در این مورد، فشار خلاء 1 برابر 50.5- (سطح 1) ، سرعت دور گرفتن 2 برابر 1.8 (سطح 2)، درجه حرارت 3 برابر 140 (سطح 4)، درجه حرارت 4 برابر 145 (سطح 4) ،درجه حرارت 5 برابر 150 (سطح 3)، درجه حرارت 6 برابر 155 (سطح 1)، درجه حرارت 7 برابر 160 (سطح 2) و درجه حرارت 8 برابر 165 (سطح 2) پارامترهای مناسب پردازش هستند. pic 10 شکل 7 (لوله مسطح) شکل 7. نشان می دهد که متغیر واکنش، قطر داخلی و ابعاد نومینال مورد نیاز شرکت هاmm 21.0 بود. بنابراین از تصویر ٧ درمیابیم که فشار خلا ١ برابر -۷.۵ ، سرعت دور گرفتن ٢ برابر ۶ و درجه حرارت های ۵،۴،۳و۶ به ترتیب برابر با ۱۲۰ و۱۳۵ و۱۲۵ و ۱۵۰ میباشد. پارامتر های فوق که در تولید لوله مسطح (ساده) استفاده میشوند ، همگی نزدیک به مقدار مورد نظر هستند. با این اطلاعات نه تنها باید پارامترهای پردازش را بهینه انتخاب کنید، بلکه باید وضعیت تاثیر آنها بر نسبت SN در نظر گرفته شود. نسبت واکنش S/N لازم است بزرگ باشد یا نباید به طور قابل توجهی برای هر نوع طراحی تجزیه و تحلیل آزمایش به حداقل برسد. در این مورد از نسبت S/N پاسخ گراف زیر فشار خلاء ۱ برابر -5.5 سرعت دور گرفتن ۲ برابر ۵.۰ و درجه حرارت های ۵،۴،۳ و۶ به ترتیب برابر با ۱۱۵ ،۱۳۵ ،۱۴۰ و ۱۵۰ میباشند که باعث میشود پاسخ سیگنال به نویز بیشتر از پارامترهای دیگر باشد . بنابراین بهتر است ،پارامتر های عملیاتی بهینه سازی و میانگین مقدار پاسخی انتخاب شود که به مقدار هدف نزدیک باشد و دارای سیگنال بزرگ باشد یا کاهش زیادی نسبت به سهم نداشته باشد. در این مورد خلاء فشار ۱ برابر -۵.۵ (سطح ۱)، سرعت دور گرفتن ۲ برابر ۵.۰ (سطح ۱) درجه حرارت ۳ برابر ۱۲۰ (سطح ۳)، درجه حرارت ۴ برابر ۱۳۵ (سطح ۳)، درجه حرارت ۵ برابر۱۴۰ (سطح ۲)، درجه حرارت ۶ برابر ۱۵۰ (سطح ۳) پارامترهای مناسب برای پردازش هستند. خلاصه ای از وضعیت عامل انتخاب شده با استفاده از طراحی یک آزمایش در جدول 4 و 5 نشان داده شده است. pic11 جدول 4 جدول 5 در اینجا با کمک از پیش بینی مقدار و مقدار میانگین واقعی ثبت شده از اطلاعات تولیدی شرکت (تجزیه و تحلیل نمودار X از تولیدات) ما این دو مقدار را تحت عنوان جدول 6 مقایسه میکنیم. ●میانگین کل خسارت=HDPE Ø 50mm● 1494.0 Birr/piece mm●5Ø2 لوله ساده = 0.0943 Birr/piece به طور خلاصه فرایند افت کیفیت قبل و بعد از استفاده از روش تاگوچی در طراحی آزمایش (DOE) در جدول زیر به طور خلاصه نشان داده شده است . pic 12 جدول 6 از جدول بالا (۶) در میابیم که درصد افت بهبود محصولات انتخاب شده از طریق استفاده از روش تاگوچی در طراحی آزمایش به طور چشمگیری بهبود یافته است. 5. نتیجه گیری از تجزیه و تحلیل نمودار X نتیجه میشود ، همه ی پروسه های تولید محصول از کنترل خارج است. بنابر این برای پیشرفت و دست یافتن به بهترین مقدار هدف باید علل آنها به حداقل برسد. با مشاهده دیاگرام علت و معلول در میابیم ، تنظیم نامناسب پارامتر های عملیاتی ، علت ریشه ای مشکلات کیفیتی(نقص) هستند. همان طور که انتظار میرود ،با استفاده از روش های تاگوچی در طراحی آزمایش برای محصولات انتخاب شده، درصد افت پیشرفت چشمگیری را نشان میدهد.این پارامتر های فرایند توصیه میشوند. بنابر این به عنوان نتیجه پردازش داده های آماری بدست آمده ، تاثیر 4 پارامتر فرایند (سرعت دورگرفتن، سرعت پیچ، فشار خلا و درجه حرارت) در فرایند های خروجی تعیین میشود. به طور کلی برای همه ی محصولات درجه حرارت از اهمیت خاصی برخوردار است. ..:: پارس اتیلن کیش نامی که سالهاست می شناسید و به آن اعتماد دارید ::..
|
پارس اتیلن کیش به کیفیت متعهد است با پارس اتیلن کیش کیفیت را تجربه کنید پارس اتیلن کیش تولید کننده با کیفیت ترین لوله ،اتصالات ومنهول پلی اتیلن در ایران شرکت پارس اتیلن کیش هیچ نماینده ای در سطح ایران ندارد و فروش لوله و اتصالات پلی اتیلن از طریق دفتر مرکزی با ارائه گواهینامه معتبر انجام میپذیرد. لوله های کاروگیت پارس اتیلن کیش، تحت لیسانس DROSSBACH آلمان تولید میگردد از شرکت هایی خرید کنید که با کارکنان ,مشتریان و محیط زیست با احترام رفتار میکنند پارس اتیلن کیش نامی که می شناسید و به آن اعتماد دارید اروپائی ها هم پارس اتیلن کیش میخرند
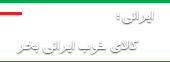